Safety & Cybersecurity
No matter how much we endeavour to accelerate further, this should never come at the expense of our employees’ safety. Working on the energy infrastructure involves risks, which is why safety is and always will be a priority, and we invest in safety measures, knowledge, professionalism and a proactive safety culture, also with regard to digital security. In this way, we guarantee the safety of our customers, employees, contractors and hired-in workers, and ensure a reliable and safe energy supply for our customers.
KPIs | Note | Unit | Result for 2022 | Target for 2023 | Result for 2023 | Target for 2024 | |
---|---|---|---|---|---|---|---|
Safety | |||||||
LTIR | Lost Time Injury Rate: Number of fatal workplace accidents + accidents leading to lost-time injuries per 1,000,000 hours worked over the past 12 months. | ratio | 0.52 | ≤ 1.90 | 0.24 | ≤ 1.50 | |
RIF | Recordable Incident Frequency: Number of fatal workplace accidents and accidents leading to lost-time injuries, requiring substitute work or requiring medical treatment per 200,000 hours worked. | ratio | 0.91 | ≤ 0.90 | 0.57 | ≤ 0.90 |
Workplace accidents
We place great importance on a safe and healthy working environment to minimise risks and prevent workplace accidents. We define workplace or occupational accidents as fatal accidents and those leading to lost-time injuries, requiring substitute work or requiring medical treatment. Our ambition is obviously to have 0 workplace accidents, but unfortunately accidents can never be completely avoided. In 2023, we achieved our target of remaining below 35 accidents. We eventually recorded 24 accidents.
In February 2022, there was a major gas accident in Zoetermeer, in which several employees were seriously injured. The investigations carried out by the Dutch Labour Inspectorate, the State Supervision of Mines (SodM) and Stedin led to a number of measures to which we gave follow-up in 2023, partly in cooperation with the sector.
What did we learn from the gas accident in Zoetermeer?
On 20 January 2023, the SodM published its conclusions of its investigation into the serious gas accident in February 2022. The SodM concluded that the direct cause of the incident could be traced back to the manner in which the work was being carried out. The proper procedures and safety rules were not followed during both preparation and execution. This conclusion has left a deep impression on us. Our customers, environment and colleagues should have the confidence that we work competently, carefully and safely.
Although our employees have extensive training, follow additional courses and receive guidance, and regular tests are carried out, things still went wrong in this case. We take this very seriously and have drawn lessons from these conclusions to prevent similar incidents in the future. We immediately acted on the points for improvement and recommendations listed in the report, among other things by including the incident and its cause as an example in our training programme. We are in close contact with the SodM about our progress in addressing the points for improvement. We completed most of the actions on these points in 2023.
The SodM also indicated that our recording system for operating assets, which among other things includes all our pipelines and cables, required improvement so as to be up to date and complete. The SodM found that the procedures followed by Stedin were inadequate to ensure that changes were implemented correctly, completely and in good time. Stedin was already in the process of improving these procedures, and stepped up this process with greater focus after the SodM report. Additional reports were introduced that provide insight into the progress on this point, which means that progress is structurally monitored.
Safety performance
We monitor our safety performance on the basis of the RIF and LTIR ratios:
RIF
The recorded RIF was 0.57, while the target was a maximum of 0.90.
LTIR
The recorded LTIR was 0.24, while the target was a maximum of 1.90.
Cause of accidents
A substantial number of workplace accidents turn out to be directly related to work, such as contact with electrical voltage or cuts and burns. Most accidents are attributable to knocks, falls and stumbling. The number of accidents due to participation in traffic has substantially decreased in recent years as a result of training.
Cause of LTIR | 2019 | 2020 | 2021 | 2022 | 2023 | ||
---|---|---|---|---|---|---|---|
At work | 0.75 | 0.13 | 0.27 | 0.39 | 0.12 | ||
Falling, stumbling, slipping | 0.50 | 0.26 | 0.13 | 0.13 | 0.00 | ||
Participation in traffic | 0.88 | 0.00 | 0.13 | 0.00 | 0.12 | ||
Total LTIR | 2.13 | 0.39 | 0.53 | 0.52 | 0.24 |
Number of lost-time workplace accidents (including contractors)
The past five years have shown a downward trend in the number of lost-time workplace accidents. We believe that this trend can be attributed in part to our efforts of raising safety awareness, both in our organisation and among our supply chain partners. We also took steps to provide temporary alternative work wherever possible as a means of keeping employees involved in work and reducing absenteeism as a result of accidents.
Number of workplace incidents without lost time (including contractors)
Total number of workplace incidents (including contractors)
This is the total number of workplace incidents with and without lost time for Stedin Group and its contractors.
Safety awareness
Within Stedin Group, Stedin Holding N.V. and DNWG Infra both obtained certification for level 4 of the Safety Culture Ladder in 2023. Stedin Holding N.V. had already been certified for level 4 last year and therefore obtained certification again in 2023. DNWG Infra advanced from level 3 to level 4 in 2023. We are immensely proud of this achievement. The Safety Culture Ladder is a standard that aims to improve safety awareness (attitude, behaviour and culture) and to make it a constant focus of attention.
Accident/incident ratio
This is the ratio between the number of accidents leading to lost-time injuries and the total number of workplace incidents.
High Reliability Organisation (HRO)
Six years ago, in order to raise safety awareness on a lasting basis, we began employing an High Reliability Organisation (HRO) programme. HRO forms the basis for a sustainable safety culture in the short and long term. The programme also contributes to reliability and predictability in the chain processes (‘first time right’). The five behavioural principles of HRO are: I think ahead - I am not afraid to ask questions and follow-up questions - I am prepared for the unexpected - I focus on solutions - I am open to the expertise of colleagues. We worked on embedding these features further in 2023.
The power of repetition
Compliance with safety regulations and guidelines requires constant attention. We therefore make sure that our employees receive safety training, which they repeat at regular intervals. They have the correct personal protective equipment and high-quality tools, which we check and approve during the annual equipment audit. In April, we held our biannual ‘Gas days’, which are intended for gas fitters. The programme addressed everyday events. In 2024, we will organise E-days for electricity fitters.
Safety in the supply chain
We involve our contractors in our health and safety system in various ways and monitor compliance with procedures through spot checks:
Registration of contractor’s personnel on site: when work actually starts, there is always a ‘start-work meeting’. We record whether employees are present on a ‘start-work form’. A ‘start-work meeting’ is standard practice for new personnel.
Procedures for presence of contractors’ personnel on work sites: only qualified personnel can be assigned work. This is done using our Electricity Business Operations (Bedrijfsvoering Electra, BVE) and Gas Business Operations (Bedrijfsvoering Gas, BVG) tool, which also contains our work and operation plans.
Safety Culture Ladder: Stedin is certified for the Safety Culture Ladder, level 4. We require level 3 from our direct chain partners, and we also ask them to advance to level 4. For other parties in the chain, the minimum requirement will be level 2 with effect from 1 January 2024.
Workplace audits: We carried out 1,904 workplace audits in 2023. We make our reports available in a secure portal, which ensures our contractors have direct access to our findings. We examine and discuss incidents and workplace accidents.
Stedin Safety Award
This year saw the sixth edition of the Stedin Safety Award, which is presented to the supply chain partner with the best safety and quality performance. The Stedin Safety Award 2023 was presented on 23 May and went to contracting firm Van Vulpen.
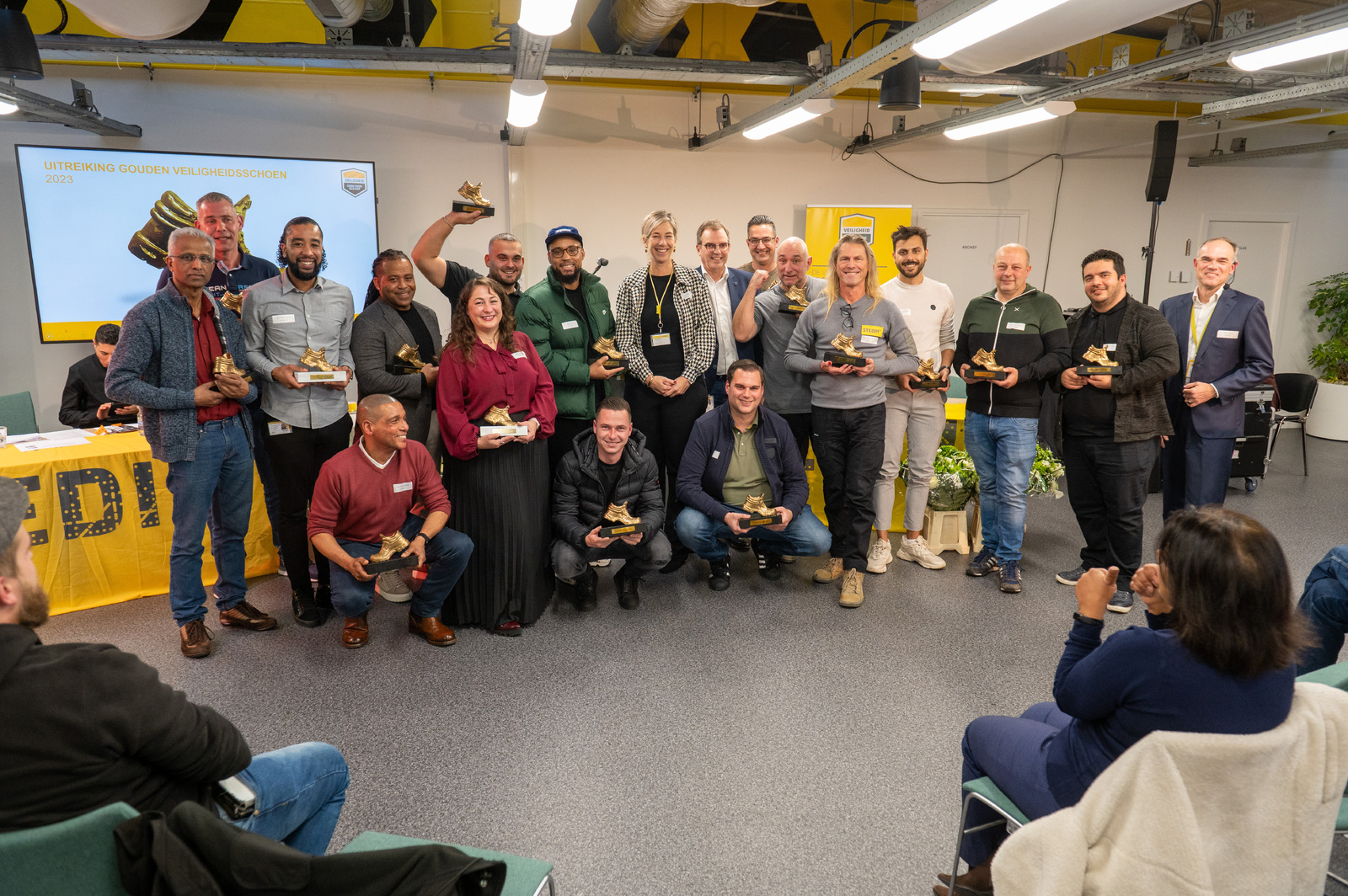
Golden Safety Shoe presentation
In November, we awarded the Stedin Golden Safety Shoe for the sixth time. We present this award as a token of appreciation for colleagues who have demonstrated a commitment to improving physical or social safety in the workplace over a long period and/or in an exceptional manner. They set an example to the organisation. The award is a token of appreciation for the person or persons in question as well as a means of promoting commitment to physical and social safety and raising safety awareness. The Golden (Social) Safety Shoes were presented to Frans Knies, Aad de Groot, Robert van den Berg, Michael Nieuwland, Ferdi Çelik, Dion Harderwijk, Hemantkoemar Jagessar-Tewari, Juan Pasquel, Dennis van Hattum, Jean Paul van Dorsselaer, Serdar Dogan, Maikel Verdonck, Rensley Maria, Gerrit Lucas, Ingnie Lenselink and Jessy Santos Frances.
Health and environment
Complying with the full range of environmental requirements and applying the correct environmental regulations in day-to-day working practice is not always easy. This is why we have set up a database for ‘non-ordinary environmental incidents’. This database serves as a practical tool for identifying situations and provides advice and insight on how to deal with the situation. In 2023, there were few situations we needed to add to the database, which indicates the database is fairly comprehensive. We monitor developments in legislation and regulations in the area of hazardous substances or pollutants, such as asbestos, benzene, sulphur hexafluoride (SF₆) and chromium (VI), which pose risks to the environment and health. For reasons of health, we encourage preventive measures such as due care, orderliness and hygiene.
Quality: certification and compliance
A good management system plays an essential role in ensuring that Stedin is a reliable and safe grid manager, whatever the circumstances. Stedin Group again demonstrably complied with the standards and guidelines in the field of safety and security, working conditions, environmental care, quality management, asset management, information security, business continuity management and crisis management in 2023.
Stedin Group certification
Stedin Holding N.V. | NetVerder | DNWG Infra |
---|---|---|
ISO 9001 (Quality) | ISO 9001 | ISO 9001 |
NTA 8120 (Asset Management) | Safety Culture Ladder, level 3 | CKB (Underground Infrastructure) |
ISO 55001 (Asset Management) | VCA** | |
VCA** (HSE) | Safety Culture Ladder, level 4 | |
Safety Culture Ladder, level 4 | ||
ISO 22301 (Business Continuity) | ||
ISO 27001 (Information Security) |
Continuous improvement
Continuous improvement (Plan Do Check Act, PDCA) is vital to improving quality. Findings from certification audits, the management review of the effectiveness of the Stedin management system, as well as inspections by regulators, provided input for the concrete implementation of continuous improvement. In 2023, we reported on improvement actions on a monthly basis to allow us to better monitor the timeliness and effectiveness of improvement actions. This approach actively contributes to our Construction, Utilisation, Management strategy.
Crisis management
In 2023, we updated the Crisis Management Plan (CMP), including with respect to ensuring adequate provision of information about crises through Grid-Centric Working and the use of the National Crisis Management System (Landelijk Crisis Management Systeem, LCMS). The LCMS facilitates rapid information sharing between all relevant parties. At Stedin, we do this using Information Coordinators (ICO).
We are further improving our crisis management organisation by providing ongoing training to the relevant target groups. For example, in 2023 we again trained new crisis managers to ensure our crisis management organisation has enough capacity. We also kept our knowledge and experience up to date by taking part in exercises, including at the national level, with other crisis management organisations such as security regions. The connection between the crisis management organisation and ICT crisis management has been strengthened. The ICT colleagues concerned have followed knowledge sessions and training courses, among other things. We also worked on the connection between crisis management and business continuity management. Exercises addressed the themes of ICT, cybersecurity and business continuity as part of the programme.
Hydrogen safety regulations
Alternative energy sources such as wind and solar energy, biogas and hydrogen are creating new opportunities and safety challenges. For example, there are no proper safety regulations yet for working with hydrogen. We are developing guidelines and regulations for hydrogen in consultation with Netbeheer Nederland.
Security and integrity
In recent years, we have increasingly experienced brazen burglaries and theft from our business vehicles and premises (in many cases involving copper theft). This has prompted us to take extensive preventive measures to secure our critical infrastructure, which also includes working closely with the police and security firms.
Fraud and an increase in aggression, threats and violence towards our employees require a considerable amount of attention. Our staff are trained to de-escalate confrontations with aggressive customers.
Energy theft and safety
Sadly, we experience gas and electricity theft for criminal purposes or personal monetary gain on a daily basis. We work closely with the other grid managers in the sector to adopt a uniform approach to tackling theft and fraud and to recover any losses we sustain. It is important to coordinate our actions in this regard with the police, municipalities and the Public Prosecution Service.
We regularly encounter energy theft by illegal cannabis growers. As the equipment they use consumes large amounts of electricity, the criminals tap energy by bypassing the meter. This almost always creates unsafe situations, and regularly causes house fires. Besides energy theft by cannabis growers, we also regularly encounter theft for domestic use.
It is estimated that 15% of Stedin’s total network losses are caused by energy theft. That is approximately 120 GWh of electricity per year. Based on the 2023 kWh price, that amounts to an estimated loss of almost € 39 million in 2023 (2022: € 25 million). Due to high purchase prices, the estimated loss in the past two years is significantly higher than in previous years. Detecting this type of energy theft is therefore even more relevant.
A total of 210 cannabis-growing operations were discovered in Stedin’s area in 2023 (2022: 264). In addition to cannabis growers, we also prioritised tackling other forms of energy theft in 2023, such as meter fraud or illegal reinforcements of connections. In 2024, we will be focusing on further grid automation to help us to proactively detect irregularities faster. We are also continuing to focus on effective cooperation with the police, the Public Prosecution Service and municipalities. Finally, we are in discussions with the Dutch anonymous crime reporting centre (M.) to increase the number of high-quality reports.
Cyber security
As the manager of part of the critical infrastructure in the Netherlands and an ‘Essential Service Provider’ under the Security of Network and Information Systems Act (Wet beveiliging netwerk en informatiesystemen, Wbni), Stedin actively and continuously takes into account a dynamic threat assessment. We proactively integrate evolving European and national legislation. Our approach is not static. We are constantly adapting to the world around us, both internally and externally. It is important to comply with legislation, but ensuring the reliability of our operations is always paramount. To this end, we apply a certified and risk-based approach according to the ISO 27001 standard, deploying our resources where they will have the most impact.
Our approach was recalibrated over the course of 2023. Our new approach involves an even stronger focus on strengthening the information security organisation, by taking steps to increase Stedin’s digital security culture. We are doing this through an awareness programme and by continuously investing in employee knowledge. Technological solutions remain essential. We continuously invest in advanced technologies to manage information security risks and protect our services from cyber threats.
Finally, cooperation with partners in both the public and private sectors is another important part of our information security strategy.